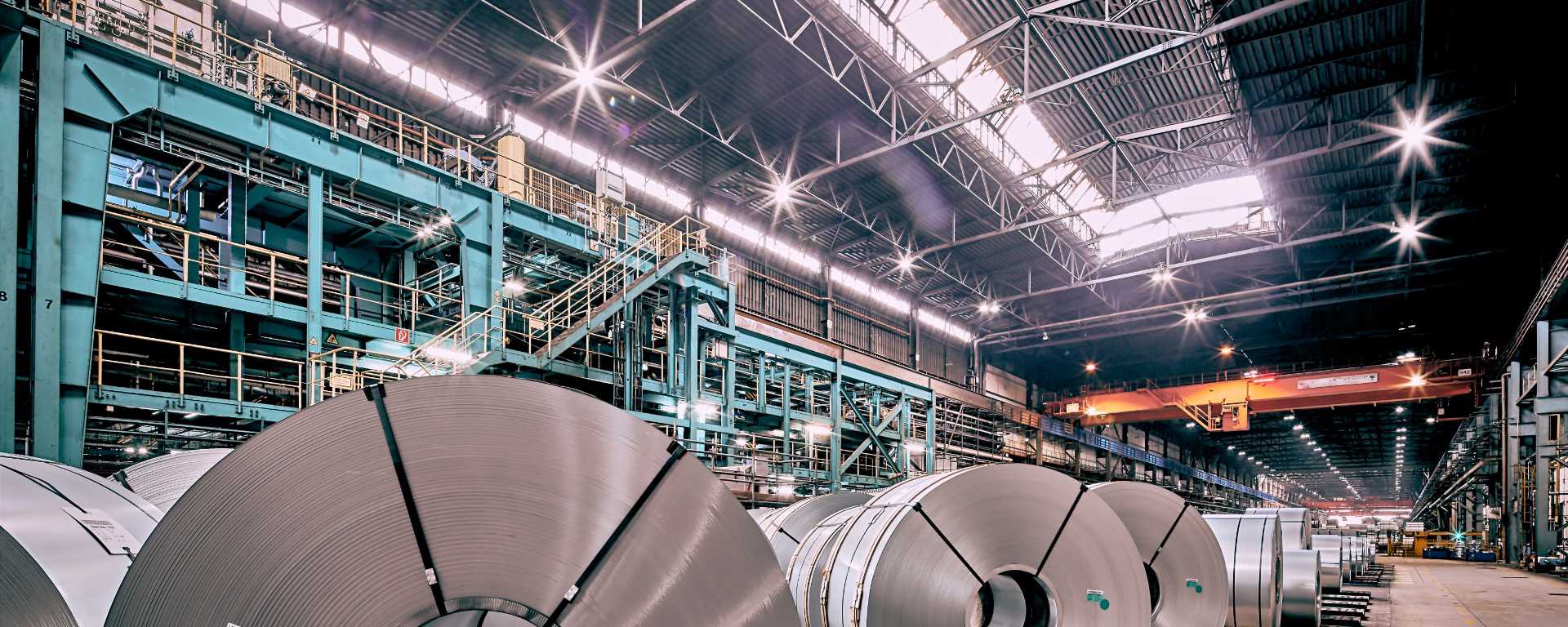
Um Stahl herzustellen, muss zunächst Roheisen produziert werden. Dies geschieht bei ArcelorMittal in Deutschland auf
zwei Wegen. Zum einen über die klassische Hochofenroute und zum anderen über das Direktreduktionsverfahren
und Einschmelzen im Elektrolichtbogenofen. Letzteres Verfahren wird in Hamburg angewandt und steht für die Zukunftsmission
einer klimaneutralen Stahlherstellung.
Hochofenroute
Aktuell stammt der überwiegende
Teil weltweiten Roheisenproduktion aus der Hochofenroute. Als Rohstoffe dienen Erz, Kokskohle und Zuschlagstoffe wie Kalkstein.
Der Hochofen wird von oben abwechselnd mit Schichten von Eisenerz und Kokskohle befüllt. Von unten wird heiße Luft
eingeblasen, wodurch Kohlenstoffmonoxid durch das Verbrennen der Kokskohle entsteht. Das Kohlstoffmonoxid wiederum lässt
die Eisenoxide unter der Bildung von Kohlendioxid zu Roheisen reduzieren, was sich in flüssiger Form unten im Hochofen
ansammelt und in regelmäßigen Abständen entnommen wird. Anschließend wird das flüssige Roheisen
im Stahlwerk weiterverarbeitet Das geschieht im Konverter durch das Einblasen von Sauerstoff. Bei diesem Verbrennungsprozess
entstehen Temperaturen von über 1.700 Grad Celsius. Als Kühlmittel wird in diesem Prozess Stahlschrott hinzugefügt,
das Material wird dem Kreislauf wieder zugeführt. In der Sekundärmetallurgie erhält der Stahl seine spezifischen
Eigenschaften, zum Beispiel durch bestimmte Legierungsmittel, mit denen sich Härte, Formbarkeit oder Korrosionsschutz
beeinflussen lassen. In der Stranggießanlage wird der Stahl in Form gegossen und in Knüppel oder Brammen zerteilt.
Danach wird der Stahl weiter in Form gebracht, entweder zu Stahlband (Flachstahl) oder zu Draht (Langstahl) gewalzt. Später
wird der Stahl zu einem Coil aufgerollt und dann an Abnehmer aus der weiterverarbeitenden Industrie transportiert.
Direktreduktionsanlage
Bei der Direktreduktionsanlage (im Hamburger Werk im Einsatz) wird
das Eisenerz zunächst zu Eisenschwamm (DRI, Direct Reduced Iron) reduziert. Dazu wird als Reduktionsmittel Erdgas
statt Koks verwendet. Der Eisenschwamm wird zusammen mit recyceltem Stahlschrott in einem Elektrolichtbogenofen (EAF)
zu Rohstahl geschmolzen. Das Reduktionsgas besteht zu rund 60 Prozent aus Wasserstoff, so dass der Schritt zu einer vollständigen
Reduktion mit Wasserstoff naheliegend ist. Wenn dieser Wasserstoff mittels Elektrolyse produziert wird, bei dem ausschließlich
erneuerbarer Strom verwendet wird, ist eine nahezu CO2-freie Prozessroute denkbar.